Just-in-time: laboratories in skyscapers for Roche
Switzerland
/
Grenzacherstrasse, Basel
2018-2024
|
F.Hoffmann - La Roche Ltd
Architect:
Herzog & de Meuron
|
Budget:
CHF 1.3 billion
The new Roche pRED Research Center for “Research an Early Development” is being built in Basel. Within four years and in the middle of a residential area, the 5000m² construction site presented us with maximum challenges. Because the whole thing happens during ongoing operations at F. Hoffmann-La Roche AG. Reduction of journeys by 40%.
emphases
BIM LEAN LOG
BIM2LOG
prefabrication
Consolidation Center
Just-In-Time
The project
The new Roche pRED Research Center for “Research and Early Development” was a mammoth project. As part of the four-billion renovation program, 15% of Switzerland's annual construction volume was used in pRED expansion at the headquarters plant of F.Hoffmann La Roche AG: The expansion volume of pRED corresponded to around 7.5 million beer crates, covering a total of 374 soccer fields.
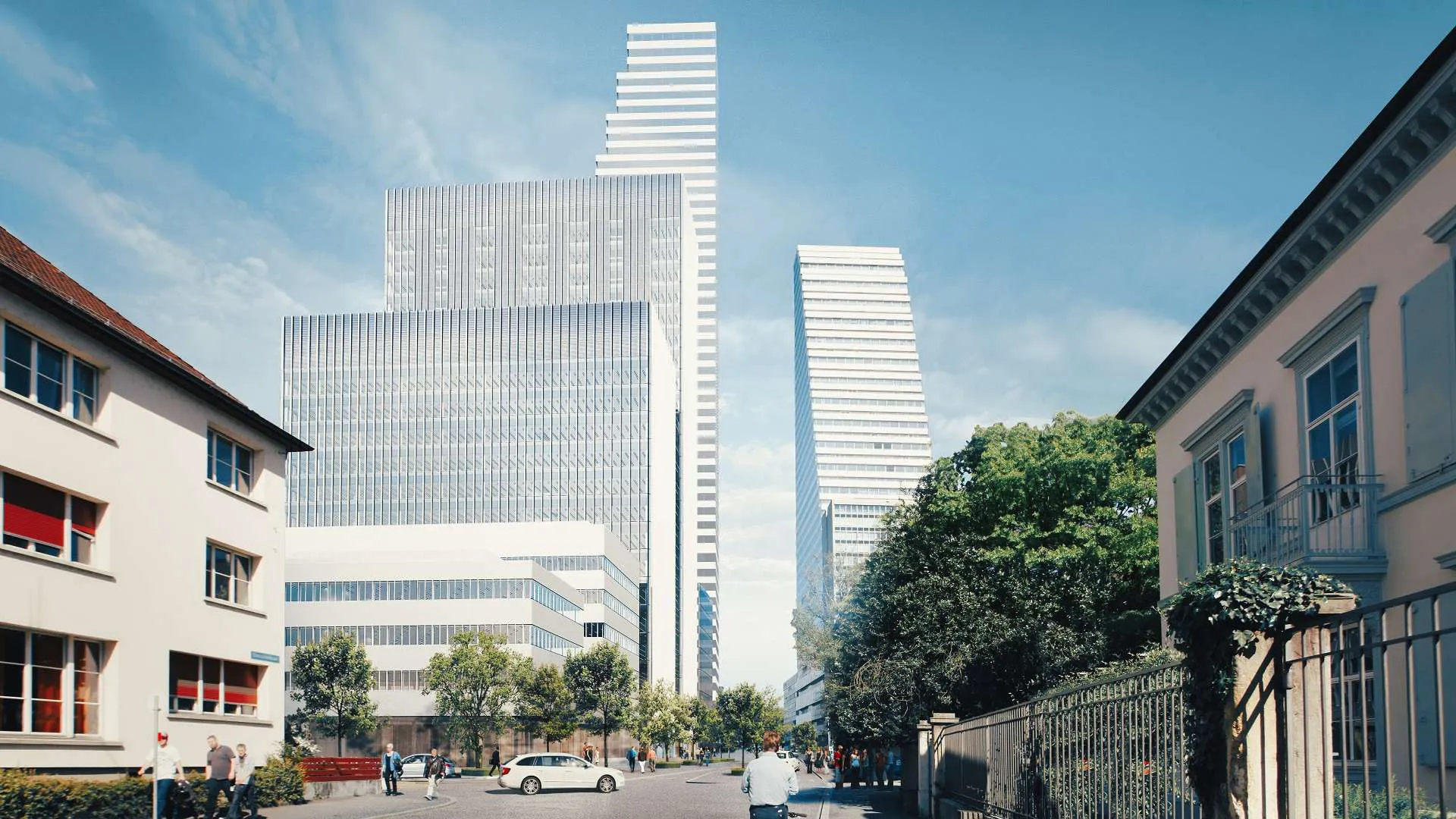
challenges
Build one of the world's most advanced laboratories in just four years — in a confined urban environment that does not allow for on-site storage space. A challenge! To solve this task for Roche, we developed a consistent logistics management system for all materials, employees and construction site equipment based on BIM (Building Information Modeling) data, Lean Construction and prefabrication. The construction site worked like a community in a very small space.
Our “construction sites”
With a height of 114 meters, Laboratory Building 7 has 25 floors. All material reached these 25 floors via lifts. In doing so, we had to overcome several difficulties at the same time.
- The amount of material
This project required around 187,000 pallets of material. - Waste disposal
The resulting waste — strictly separated into wood, cardboard, foil, stone, of course — had to be disposed of from the floors in roll containers. - The parallelism of construction
Problem: While the first laboratory has already been set up in the lower area, work was still being done on the shell in the upper section. This meant that the lift shaft wasn't finished yet. Solution: Lifts in the building were provisionally led up to predefined false ceilings. In addition, outdoor lifts were installed outside the façade. - The number of workers
Problem: At times, 1500 people worked on the construction site at the same time. They all needed food and access to sanitation facilities. Even if everyone only left the building once a day, the lifts would be blocked over long distances. Solution: Meals were served on the upper floors. Sanitary facilities were available at various levels.
solution
Just-in-time
If there is no storage space on site, there is just one solution: Just in Time (JIT). With JIT, exactly as much material is brought to the area as can be processed there. The information from BIM provided us with exact information on the quantity of material and destination as well as the type of work — in connection with Schedule (BIM2LOG) We were able to ensure that the right material arrives at the right place at the right time.
Consolidation Center
In upstream Consolidation Center goods were delivered and assembled to bring them to the construction site “just in time”. Pre-assembly and modular construction also took place here away from the construction site. For example, ceiling installations that were assembled in advance for installation and brought onto the floors in specially designed containers. This consolidation center was the first of its size with prefabrication in Switzerland.
logistics service
Efficient logistics services were essential for the successful implementation of our concept. In close cooperation between our specialist construction management and an experienced logistics service provider, Swiss Post, we finally successfully implemented this pilot project. Our careful planning and coordination with the client was the basis on which Swiss Post implemented the project. Through continuous controlling and quality management, we were able to ensure smooth implementation.
Procurement and removal logistics
Roche stores goods and equipment at various locations in Basel. This is both an existing and new product. This had to be catalogued and moved into the new rooms. In order to guarantee a smooth process here, we developed the MOVEit APP. She helped to catalog goods at your storage locations and made them trackable via QR code. Using Data Analytics (DCL) We then determined which goods had to be moved when and where. The challenge was that the highly specialized experts required to start up certain devices worked worldwide and were only available to a limited extent. Our solution: targeted programming of the algorithm. A first for the industry: For the first time, a schedule was created from a computer calculation.
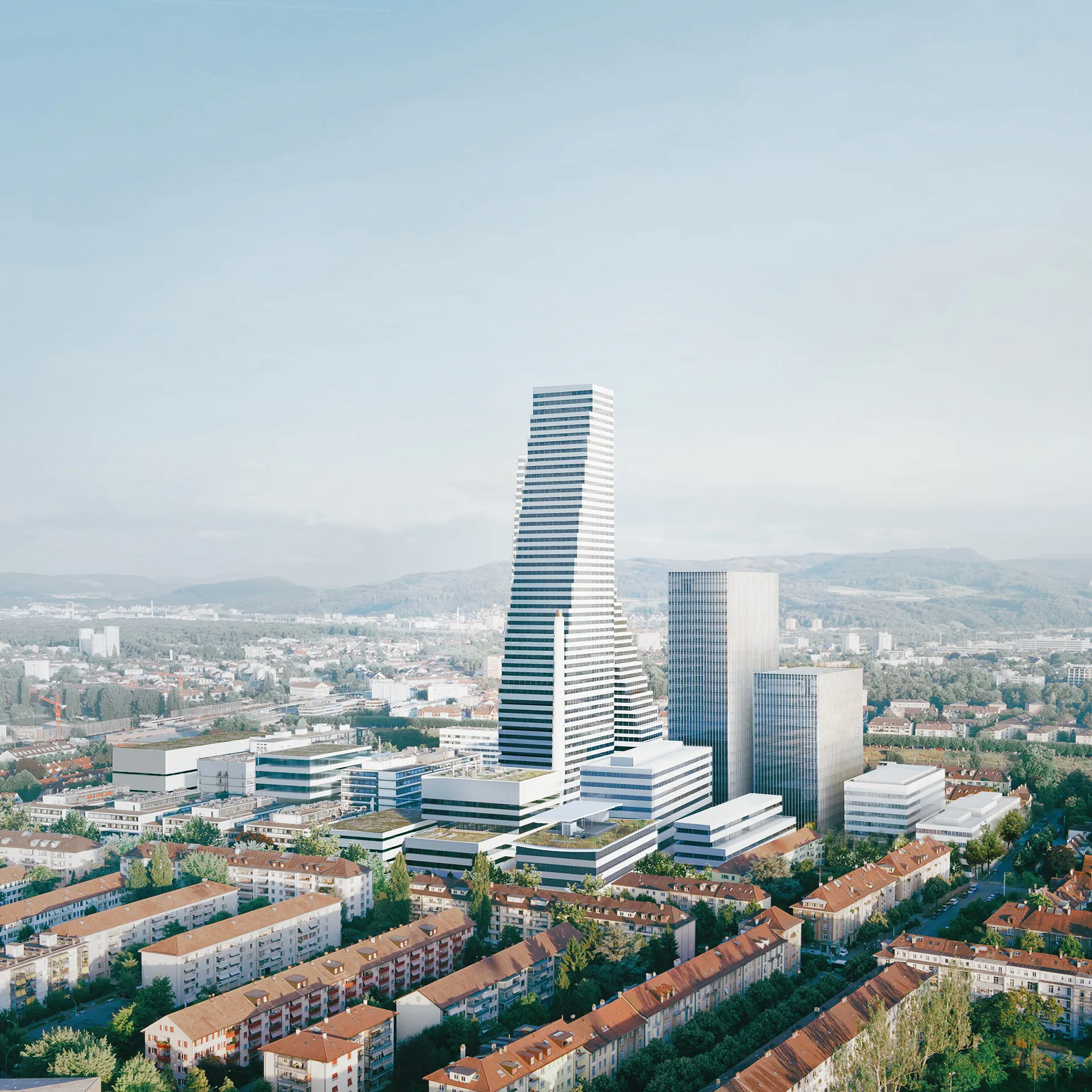
“The prefabrication of selected modules is a key factor in ensuring that we are on schedule with our challenging project.”
scores
With the help of the consolidation center, we massively reduced complexity on the construction site and were also able to largely avoid disruptions. Direct trips to the construction site were reduced by 40% as they could be handled at the consolidation center. In total, we recorded up to 80 truck movements per day at the consolidation center — that's 70% of all deliveries. The remaining 30% were delivered directly to the construction site. The trips between Consolidation Center and construction site took over environmentally friendly electric trucks. We did pioneering work in the area of data-driven scheduling: An algorithm controlled the procurement of laboratories.
Further successes/Positive side effects
- Reducing emissions from electric trucks
- Higher efficiency of deployed personnel through centralized elevator management
- Improving motivation and focusing on the essentials by reducing chaos
- Significant reduction in absenteeism due to a better working environment and less stress
- Increasing added value through reliable schedules and good use of infrastructure
- Saving several tons of scrap material, as incorrect cuts and incorrect deliveries were reduced. As a result, fewer delivery trips were necessary.