BF1 Campus Suurstoffi: true pioneering achievement thanks to BIM-LEAN LOGISTICS
Switzerland
/
Suurstoffi 1–6, Risch-Rotkreuz
2019—2021
|
Zug Estates Holding AG
Architect:
Büro Konstrukt AG Architekten, Manetsch Meyer Architekten AG
|
Budget:
CHF 185 million
The combination of the Building Information Modeling (BIM) working method with lean construction and logistics made it possible to meet the tight schedule for the new campus of the Lucerne University of Applied Sciences and Arts in Risch-Rotkreuz. Two of the three buildings were built using a hybrid timber construction method, the planning of the wooden elements was based on 3D models.
emphases
BIM-LEAN LOGISTICS
Process-controlled construction logistics
Space management
Just-in-time
The project
The new campus of the Department of Computer Science at Lucerne University of Applied Sciences and Arts has been built on the Suurstoffi Campus. “Baufeld 1”, located right next to the Rotkreuz train station, consists of three new buildings, including the “Arbo”, the highest wooden high-rise building in Switzerland. The three new buildings offer a total of 26,000 square meters of rentable office and commercial space. In addition, the sustainable mixed-use development will provide space for around 1500 residents, 2,000 students and over 2500 jobs in the future.
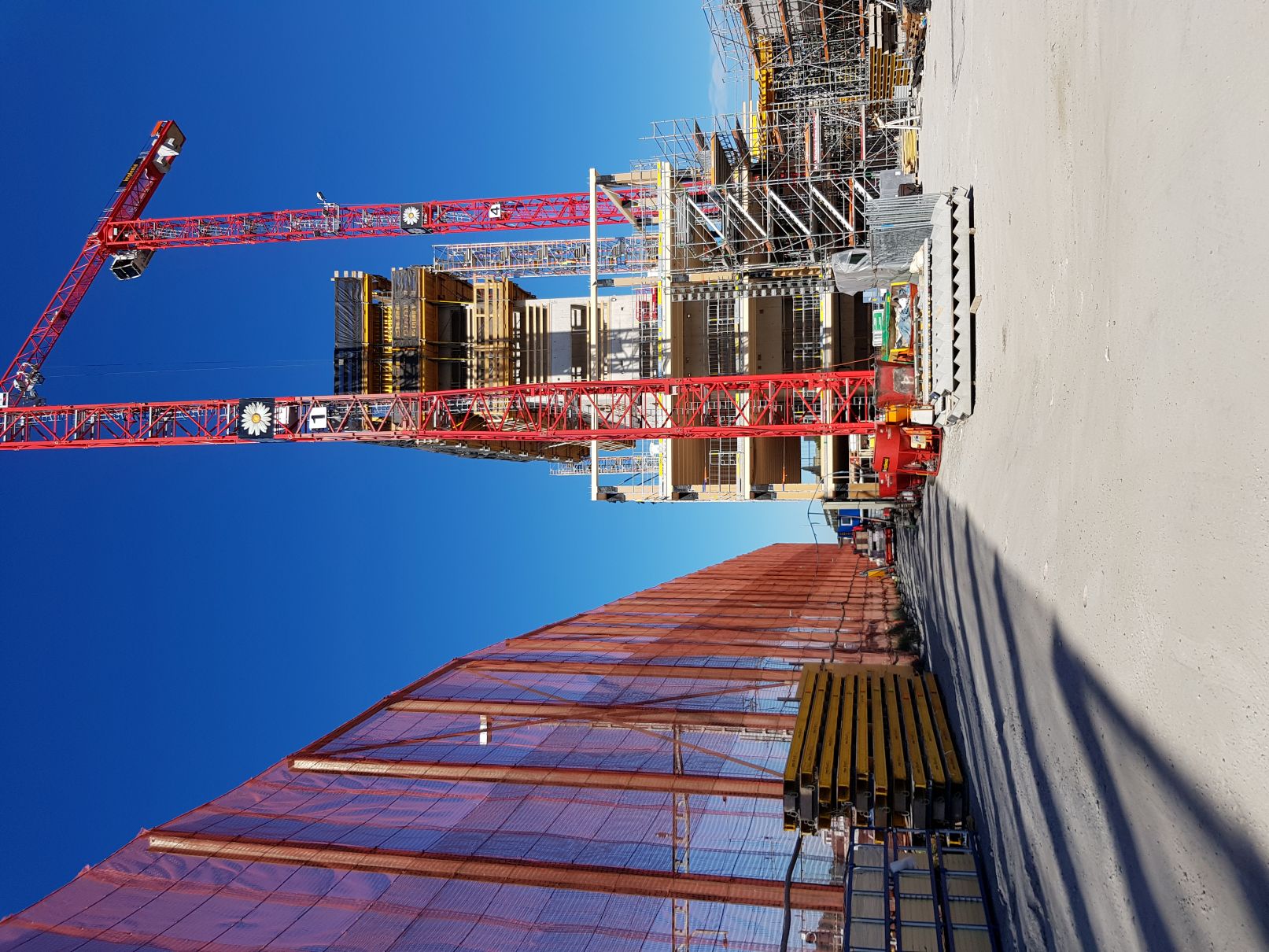
challenges
The “Construction Site 1” project on the Suurstoffi Campus imposed various high demands on planning, coordination and logistics. On the one hand, it was necessary to ensure planning security throughout the entire process — this was because 260 project participants from 40 companies had to be coordinated during the construction phase. Another challenge was ensuring a central communication structure. In addition, the integration of BIM, LEAN and LOGISTICS required continuous digital networking. Just-in-time deliveries had to be precisely timed to avoid bottlenecks. But flexibility was also crucial in order to be able to react quickly to deviations and to smoothly control the construction process.
solution
In order to manage complex processes efficiently, BIM and lean methods were used. Model-based planning enabled precise coordination of all processes, while a project monitoring tracked progress in real time and facilitated adjustments.
A central digital 5D model served as an interface for all relevant information, including logistics data on loading and unloading areas, disposal zones, and storage and buffer areas. These were linked directly to BIM via an interface, so that all participants — from planning to implementation — were integrated into a central lean management system. As a result, transports, material flows and work processes could be seamlessly coordinated.
During the construction phase, the system automatically optimized the logistics zones and lay-down areas and suggested the most efficient use of the space to dispatchers in real time. The logistics tool recorded and managed just-in-time deliveries, with an automated approval process efficiently covering the entire material flow. Lean cards in the logistics system were used to display delivery times and material information in accordance with board planning. Dispatchers also always received up-to-date construction site installation plans and precise weather forecasts to optimally manage delivery.
Thanks to real-time tracking, transport routes and time windows could be flexibly adjusted to avoid delays. Individualized dashboards ensured full transparency and predictive control of the entire delivery and assembly processes. This digital integration enabled everyone involved to keep track of things, identify bottlenecks early on and coordinate resources efficiently. This ensured a smooth, timely implementation of the major project.
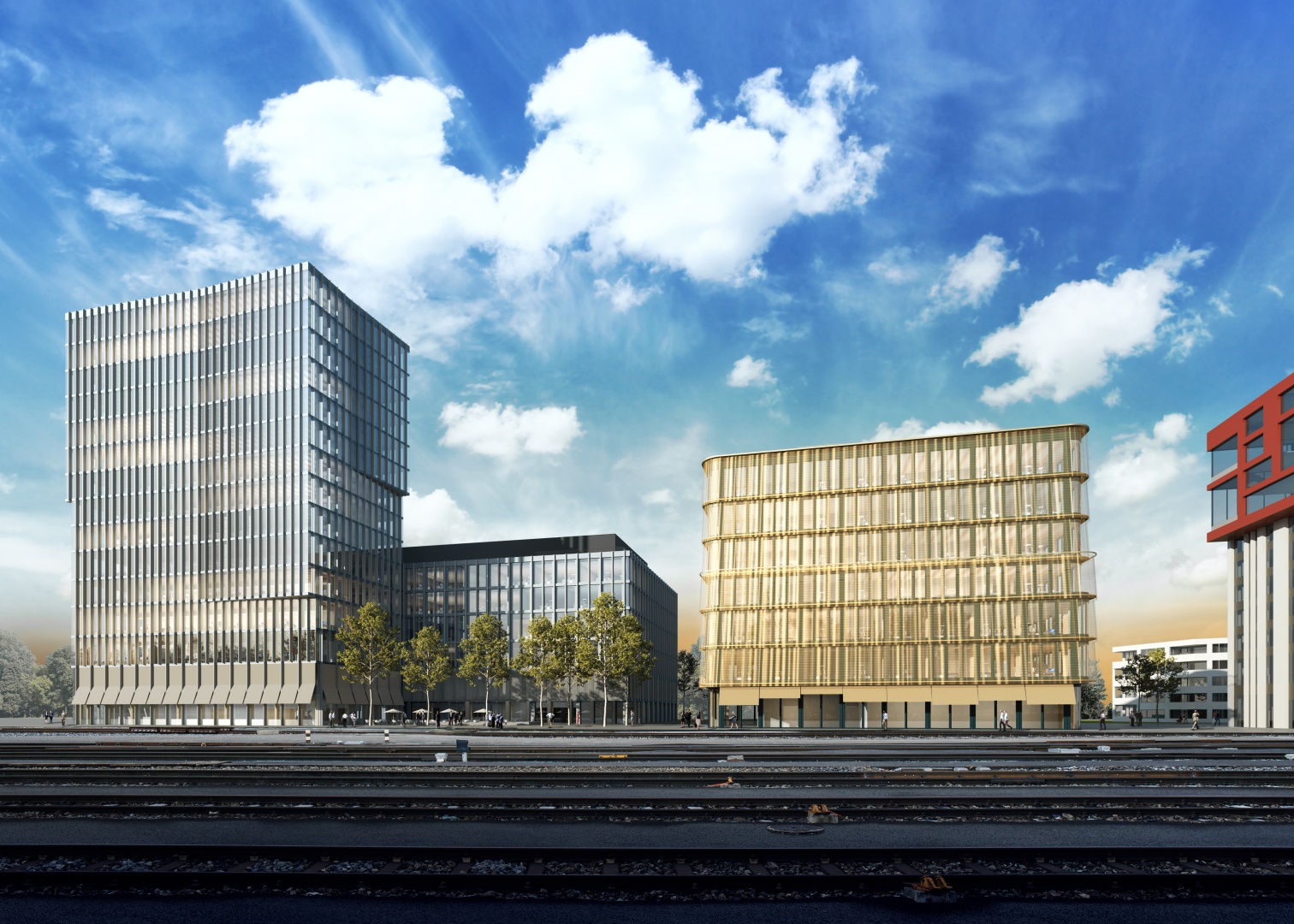
«Digital construction combined with lean management and a logistics app has reduced the construction period of the campus by one year.»
scores
The implementation of BIM and lean methods not only increased timeliness, but also transparency throughout the construction process. Careful daily planning and optimized collaboration, which was significantly improved by working together on the 3D model, were crucial for this success. Without the integrated synergy of BIM, lean and logistics, these remarkable results would not have been possible. All of these factors make this project a pioneering achievement in model-based planning and construction.